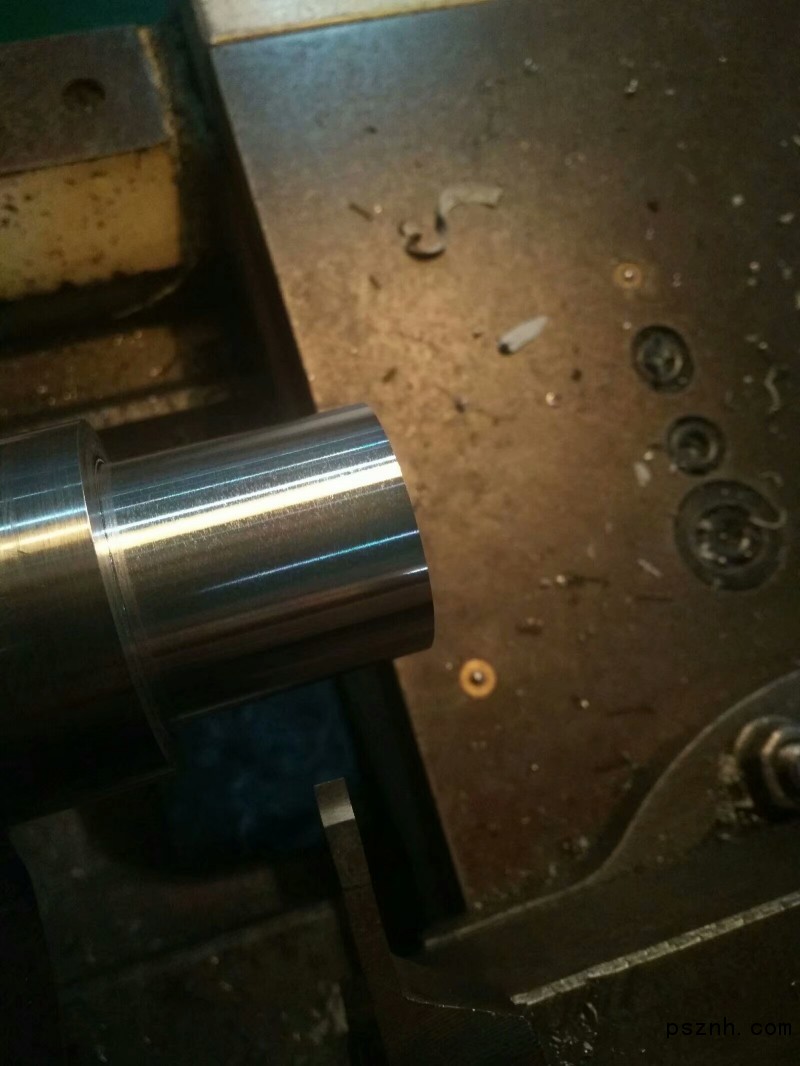
1.操作方法
把工件端面和外圆都切削一刀(端面平,车外圆),然后测量外圆直径D;换粗车螺纹刀切削螺纹。具体方法如下:
把粗加工刀具(T0x00)用手摇脉冲发生器先对切削加工后的外圆D。用手摇脉冲发生器在Z轴正方向摇出工件,输入D值(此把刀X轴对刀完)。记下X轴显示的具体数据。用手摇脉冲发生器在X轴所显示记录的数据上向负方向进给1~2mm。同样用手摇脉冲发生器在Z轴负方向进给,刀具切削到工件即可。输入Z0(Z轴对刀完)。这时粗车螺纹刀具对刀结束。
按此方法再对螺纹精加工,操作步骤和粗车刀具对刀方法完全一致。这样就不会在切削过程中产生乱扣现象。即使有更多把刀具切削加工,也同样不会产生乱扣现象。
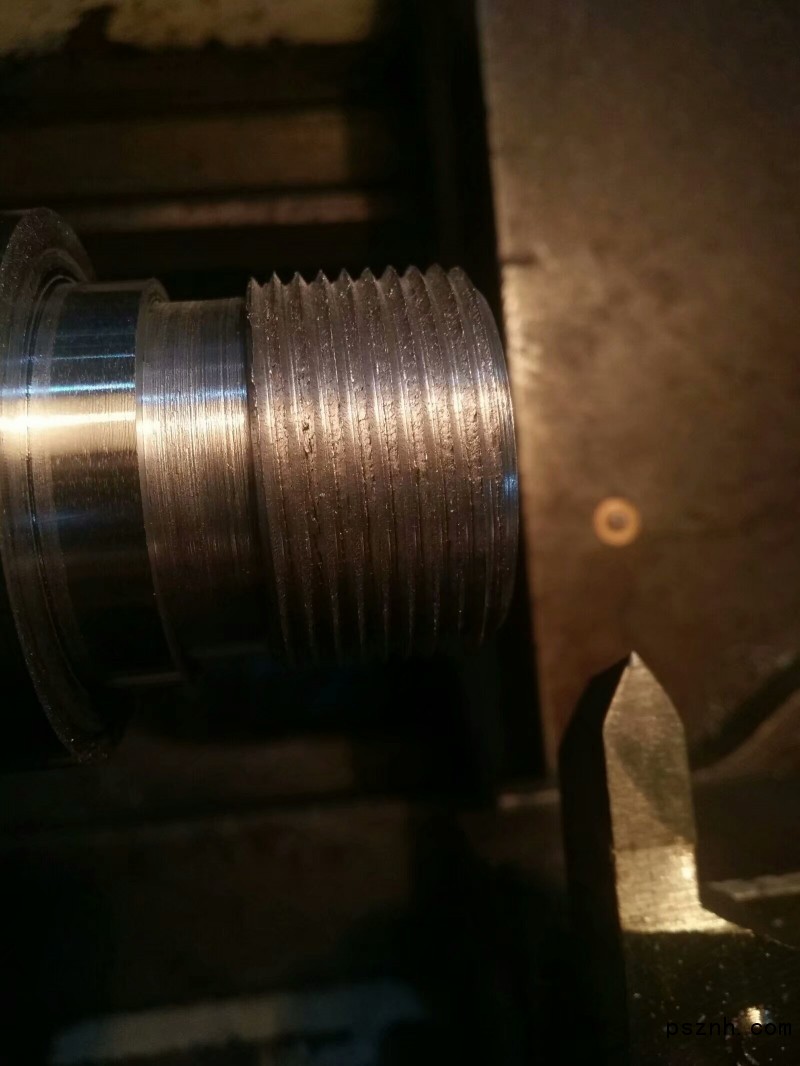
2.注意事项
(1)各把刀具在对X轴时,机床显示的数字各不相同。一定要记录好各把刀具的实际数据。在退出X轴后,多把螺纹切削刀具X轴进刀的数据一定要相同,不能有差异。
(2)在对刀的过程中,接近工件X轴和Z轴时,建议手摇脉冲发生器最好选择进给量0.001mm挡位。
(3)、车削台阶轴时,为了保证车削时的刚性,一般应先车直径较大的部分,后车直径较小的部分。
(4)、在轴得工件上切槽时,应在精车之前进行,以防止工件变形。
(5)、精车带螺纹的轴时,一般应在螺纹加工之后再精车无螺纹部分。
(6)、钻孔前,应将工件端面车平。必要时应先打中心孔。
(7)、钻深孔时,一般先钻导向孔。
(6)、车削(Φ10—Φ20)㎜的孔时,刀杆的直径应为被加工孔径0.6—0.7倍;加工直径大于Φ20㎜的孔时,一般应采用装夹刀头的刀杆。
(8)、车削多头螺纹或多头蜗杆时,调整好交换齿轮后要进行试切。
(9)、使用自动车床时,要按机床调整卡片进行刀具与工件相对位置的调整,调好后要进行试车削,首件合格后方可加工;加工过程中随时注意刀具的磨损及工件尺寸与表面粗糙度。
(10)、在立式车床上车削时,当刀架调整好后,不得随意移动横梁。
(11)、当工件的有关表面有位置公差要求时,尽量在一次装夹中完成车削。
(12)、车削圆柱齿轮齿坯时,孔与基准端面必须在一次装夹中加工。必要时应在该端面的齿轮分度圆附近车出标记线。